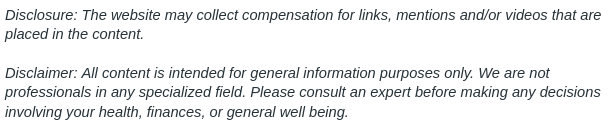
Rotary feeders, often an essential component in various industrial processes, serve to control the flow of materials from one chamber to another. Understanding the different types of rotary feeders and their applications can help optimize your operations. In this article, we will explore the top types of rotary feeders and answer some of the most common questions about them.
What Are the Main Types of Rotary Feeders?
Drop-Through Rotary Feeders
Drop-through rotary feeders are designed to allow materials to pass through a central inlet and exit through a bottom outlet. They are particularly effective in handling dry, free-flowing materials like grains and powders. Industries such as agriculture, food processing, and pharmaceuticals commonly use drop-through rotary feeders. Their straightforward design makes them easy to maintain and reliable for consistent operation. The use of drop-through rotary feeders enhances efficiency by providing precise control of material flow. This results in smoother operations and minimizes the risk of bottlenecks in production lines.
Blow-Through Rotary Feeders
Blow-through rotary feeders feature a unique design where air is used to assist in the transfer of materials. This design reduces friction and clogs, making them ideal for fine powders and granular materials. Industries such as plastics, chemicals, and cement benefit from the high efficiency of blow-through rotary feeders. Their ability to handle difficult materials with precision makes them highly valuable in these sectors. By reducing the need for mechanical components to manage flow, blow-through rotary feeders minimize maintenance costs. This reduction in operational costs can significantly improve the overall profitability of production processes.
How Do Rotary Feeders Enhance Efficiency in Industrial Applications?
Improved Material Handling
Rotary feeders enhance efficiency by streamlining material handling processes in various industries. They ensure a consistent and controlled rate of material flow, which is crucial in maintaining production balance. Efficient material handling prevents downtime and reduces the likelihood of equipment malfunctions. This reliability helps increase overall productivity in complex manufacturing environments. With rotary feeders, businesses can achieve more accurate metering of materials. This precision reduces the consumption of energy and resources, aligning with environmental sustainability goals.
Reducing Material Waste
One of the major advantages of employing rotary feeders is their ability to significantly reduce material waste. Since they provide controlled metering, they prevent excess material from spilling or being improperly processed. Reducing material waste is not only cost-effective but also aligns with modern sustainability practices. It allows companies to produce more with less, thus optimizing the use of resources and reducing environmental impact. A fact worth noting is that optimized material handling using rotary feeders can improve yield in manufacturing processes. This improvement translates to better product quality and consistency, meeting consumer demands more effectively.
What Materials Can Be Used with Rotary Feeders?
Common Materials
Rotary feeders are compatible with a wide range of materials including powders, granules, grains, and pellets. Each material requires specific handling characteristics that rotary feeders are capable of managing effectively. The most common industries utilizing rotary feeders for these materials are agriculture, food processing, plastics, and pharmaceuticals. By offering versatility, they become an integral part of diverse production lines. The consistent operation of rotary feeders with these materials ensures reliable production schedules. This consistency is crucial for meeting the demands of high-volume production environments.
Specialized Applications
In specialized applications, rotary feeders handle unique materials that require careful consideration. Materials such as chemical dusts, harsh minerals, and fine particles necessitate specialized feeding solutions. Industries that deal with chemicals, energy generation, and cement production utilize rotary feeders for these challenging applications. Their design adaptations are pivotal in maintaining safety and efficiency in processing these materials. Rotary feeders in specialized applications often come with additional features such as wear-resistant coatings and advanced sealing technologies. These enhancements ensure a longer lifecycle and reduced maintenance costs.
What Factors Should Be Considered When Selecting a Rotary Feeder?
Capacity and Size
When selecting a rotary feeder, one of the primary considerations is capacity and size. The right feeder should match the material throughput requirements of the application to avoid undersizing or oversizing. Considering the size of the feeder in relation to the available installation space is essential. Proper fit ensures seamless integration within existing process lines, promoting efficient operation. Choosing the wrong capacity can result in operational inefficiencies and increased wear and tear on the equipment. Therefore, careful analysis of production needs is required to make an informed decision.
Material Compatibility
Material compatibility is a critical factor in the selection of rotary feeders. Ensuring that the feeder is constructed with materials compatible with the substances it will handle is imperative to prevent contamination and equipment degradation. This compatibility extends to considering chemical resistance and temperature tolerance. Industries that handle corrosive or high-temperature materials must select feeders designed to withstand such conditions. Rotary feeder manufacturers offer a variety of materials and coatings to enhance compatibility with specific applications. Customizing the feeder construction based on material properties helps optimize performance and longevity.
Understanding the different types of rotary feeders is crucial for improving efficiency and optimizing material handling in industrial applications. By selecting the appropriate rotary feeder, businesses can reduce waste and enhance production processes. Evaluating factors such as capacity, size, and material compatibility will enable informed decision-making when it comes to choosing the right rotary feeder for specific needs.